VIDOK is a renowned Polish manufacturer of windows and doors made of wood, PVC and aluminium. Throughout the years, the company has grown from a small office to a well-known manufacturer selling its products all over the world. The company constantly improves its products and increases its competitiveness. In the production process, it uses the latest technologies that affect the innovation of the manufactured joinery.

- Implementations
- VIDOK - Case Study
Implementation of Stolcad® Professional with drivers for managing the production line and modules for production automation at the VIDOK company - Case Study
About the VIDOK company
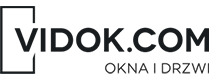
Stolcad® program at VIDOK
VIDOK has been producing and offering products with the use of Stolcad® program for over 20 years. The company is also one of the oldest users of Stolcad® Professional, as they have been working on a more and more modern version of the program every year since 2014. Not only does VIDOK work on the standard program version but they also use a wide range of the additional modules, a lot of drivers, as well as individually coded extensions and interfaces.
The production line of a new generation
The VIDOK company owns modern PVC production lines fully controlled by Stolcad® Professional. The extensive production line includes a set of machines: cutting centres, PVC and steel machining centres, many four-head welding and cleaning lines, saws for glazing beads and many other machines. Drivers made by us as well as the module to Stolcad® Professional for cutting and processing PVC profiles include operating the full set of the machines. In this project, the cutting centre connected to the machining centre carries out operations on frames, sashes and fixed posts. The scope of the performed operations depending on the profile type is as follows: many different marking, drilling and milling operations for window and door fittings, drainage and venting, ventilators, various post connectors, marking for dowels.
The steel machining centre operates on PVC profiles with the steel already set in the position. Modern welding machining lines which do not require corner cleaning can perform welding on both frames and sashes. The important part of this project was not only to control the machines, but also to do it in such a way that the line as a whole would be as efficient as possible. It required a joint analysis of each machining detail on individual machines depending on the type of the product and the technology in which they were to be made. Hence, we introduced the original software solutions in Stolcad® Professional, dedicated to the specificity of daily work in VIDOK. They required automatic divisions of the components of the finished products and their optimal distribution in the production hall. Please, find some of them described below.
Data synchronization between the program and the machines
Synchronization of the data transmitted to the individual machines is necessary for the consistent operation of the entire line. For this purpose, Stolcad® Professional arranges the order of all elements with barcodes. The technologist gained the functionality of the automatic division of the selected orders (from the production on a given day) into production packages, and transferring them to all the machines with just one click. The set of logistic modules allows, among others, planning the performance of each individual production line in window units.
It is possible to define criteria for passing windows to individual production lines. For example, shaped windows for the non-standard line, oversized windows also for the non-standard line, other windows for the standard line. The program divides orders into consecutive lines for individual working days at the same time informing how much free production capacity is available on a given line on a given day. The operator can quickly pass windows between lines and days at any time. With these features, one does not need to divide large orders manually.
Division of orders based on available carts
Automatic division into production packages with regard to trolleys is necessary to maintain the smoothness of the production. It is based on the fact that the driver automatically divides the daily production batch into packages depending on the size of the trolleys. For example, if the trolley fits profiles for 20 packs and one allocates one trolley for frames and two trolleys for sashes, the entire daily production will be automatically divided into packages of no more than 20 frames and no more than 40 sashes in one package in such a way that one package will always contain complete windows. The use of this module allows for the effective use of trolleys for cut profiles and shortening the time of production preparation by office employees.
Modern paperless production
The module of Stolcad® Professional for production viewing allows displaying information for employees in the hall what kind of elements have to be installed at a given workstation, and remotely preview the conducted stages. For example, after scanning the sash at the sash fitting workstation, the information on which casement bolt and extension should be installed on a given sash will be displayed. If a hinge up to 130 kg should be mounted on the sash from the example, such information will appear. Another example: at the glazing workstation after scanning the window label, the information which panes and glazing beads have to be installed in this window appears.
The configurator built into Stolcad® Professional decides which elements and on which workstation should be displayed. The VIDOK company has adapted the module to analyse the production at the key production stations: "Cutting and processing", "Welding", "Initial frames fitting", "Fitting the posts", "Initial sash fitting", "Fitting the sash_1", "Fitting the sash_2", "Patio fitting", "Window assembling" and "Quality control". This extension is complemented by the Production Monitoring Module, which enables remote tracking in Stolcad® Professional at what stage each window is produced.
Summary
The VIDOK company always uses the full spectrum of Stolcad® Professional program. In this case study, we presented the implementation of Stolcad® Professional with drivers for managing the production line and modules for production automation. In addition to this project, we have been implementing many IT solutions dedicated to the specificity of VIDOK's work.
Currently, i.e. in the year 2022, we are implementing the latest extension of QR Code Module for the Production Label Module in VIDOK. This option allows generating personalized QR codes that can be placed on labels or other documents. An example of the use of QR codes is the easier identification of the construction during a potential complaint process.
